Протяжка металла - технологический процесс изменения геометрии и свойств металлических изделий. Узнайте, как она улучшает характеристики материала и какие методы применяются. Читайте на Привет, вязание!
Cодержание
Протяжка металла - это технологический процесс, используемый для изменения геометрии и свойств металлических изделий путем их деформации пластическим способом. Этот процесс позволяет улучшить характеристики материала, такие как прочность, твердость, усталостная стойкость, а также добиться более точной формы и размеров деталей. Протяжка может использоваться в различных областях промышленности, включая машиностроение, авиастроение, автомобилестроение, а также при изготовлении просечно-вытяжных листов.

Методы работы
Процесс обычно выполняется на специальных станках, называемых прессами. В зависимости от требуемых характеристик изделия, а также его начальной формы, могут использоваться различные методы.
1. Холодная протяжка:
Для материалов, которые хорошо поддаются пластической деформации, этот метод проводится при комнатной температуре. Заготовка подвергается давлению и деформации через специальные матрицы или матрицы с порядковой протяжкой, чтобы получить желаемую форму и размер.
2. Теплая протяжка:
Для менее пластичных металлов процесс может проводиться при повышенных температурах. Это улучшает пластичность и уменьшает сопротивление деформации.
3. Горячая протяжка:
Применяется для материалов, которые отличаются пластичностью при высоких температурах. Металлическая заготовка подогревается до определенной температуры и деформируется через матрицы.
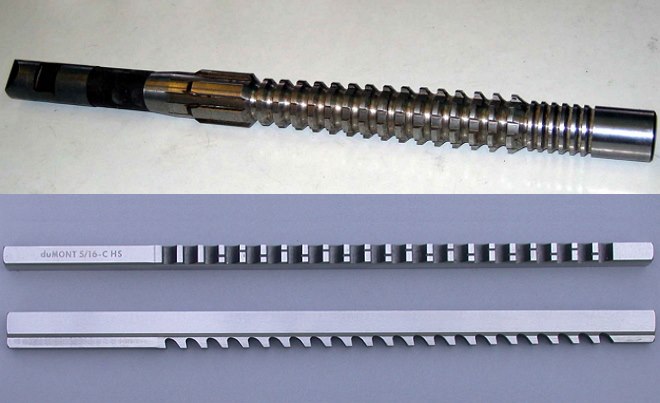
Этапы процесса
Процесс протяжки металла состоит из нескольких этапов:
1. Подготовка:
Прежде чем начать процесс, необходимо подготовить металл. Заготовка может представлять собой кусок определенной формы и размера. Этот этап также может включать предварительную обработку, например очистку от загрязнений и окислов.
2. Подогрев:
Для многих металлов, особенно при проведении горячей протяжки, подогрев до определенной температуры является важным этапом. Он увеличивает пластичность материала, уменьшая его сопротивление деформации и облегчая дальнейший рабочий процесс.
3. Протяжка:
Этот этап является центральным в процессе. Подготовленная и, при необходимости, подогретая заготовка помещается между двумя матрицами с определенной формой и размером отверстия. Затем на материал оказывается давление с помощью гидравлических прессов или других устройств. В результате давления он пластически деформируется, изменяя свою форму и размер в соответствии с формой отверстий в матрицах.
4. Охлаждение:
После предыдущего этапа материал может быть охлажден путем погружения заготовки в воду. Охлаждение позволяет закрепить новую форму металла и уменьшить внутренние напряжения, которые могли возникнуть в процессе.
Протяжка металла является эффективным способом обработки металлических изделий. Она позволяет достичь желаемых характеристик материала и улучшить качество деталей. Протяжка может быть выполнена в различных режимах, в зависимости от требуемых характеристик и материала. Этот процесс имеет несколько этапов, включая подготовку, подогрев, протяжку и охлаждение. Применение протяжки металла широко распространено в различных отраслях промышленности.
См. также
Что нам скажет Википедия?
Протяжка — многолезвийный инструмент с рядом последовательно выступающих одно над другим лезвий в направлении, перпендикулярном к направлению скорости главного движения, предназначенный для обработки при поступательном или вращательном главном движении лезвия и отсутствии движения подачи.
В зависимости от вида протягивания — наружного или внутреннего — различают, соответственно, наружные и внутренние протяжки.
Протяжки позволяют обрабатывать фасонные поверхности. Форма поверхностей, на практике протягиваемых чаще других, является одним из критериев классификации протяжек, то есть принято протяжки разделять на шпоночные, круглые, шлицевые, квадратные и т. д. Если же за один рабочий ход протягивается ряд типовых поверхностей, то осуществляющая его протяжка является комбинированной.
В соответствии со схемами резания при протягивании различают протяжки профильной (обычной), генераторной (ступенчатой) и групповой (прогрессивной) схем резания.
Разновидностью протяжного инструмента являются прошивки, применяемые для обработки отверстий, пазов и других поверхностей. В отличие от протяжки, работающей на растяжение, прошивка работает на сжатие и продольный изгиб. Для прошивания отверстий применяют механические и гидравлические прессы.
Существуют и другие виды протяжек. Так, в силу того, что протяжка является режущим инструментом, некоторые классификационные признаки режущего инструмента вообще могут быть в частности положены и в основу классификации протяжек. Например, как многие виды режущего инструмента, протяжки бывают цельными и сборными.
Конструктивные элементы внутренних протяжек
Внутренняя протяжка имеет следующие конструктивные элементы: хвостовик с длиной l1, служит для закрепления протяжки в патроне протяжного станка и передачи силы резания, шейку длиной l2, переходный направляющий конус длиной l3, переднюю направляющую l4, рабочую часть длиной l5, которая состоит из участков длиной l6 с черновыми зубьями, длиной l7 с чистовыми зубьями и участка l8 с калибрующими зубьями, заднюю направляющую часть длиной l9 и задний хвостовик l10.
На рабочей части протяжки (длина l5) расположены черновые, чистовые и калибрующие зубья. Чистовые зубья имеют меньший подъем зуба, чем режущие. Режущие зубья предназначены для снятия основного припуска с обрабатываемой поверхности заготовки. Подъем на зуб Sz определяется в зависимости от типа протяжки и обрабатываемого материала. Форма режущих зубьев в сечении, проходящем через ось протяжки. Режущие кромки обычно расположены в плоскости, перпендикулярной к оси.
Расстояние между лезвиями режущих зубьев, то есть шаг р, является одним из основных размеров, определяющих конструктивные элементы, конструкцию протяжки и ее работоспособность. Между зубьями расположены стружечные канавки. Форму и размеры зуба и стружечной канавки устанавливают исходя из условий возможности резания и образования стружки, размещения стружки в канавке и прочности зуба. Они зависят от шага зубьев р, высоты hк стружечной канавки, ширины b спинки зуба, переднего γ и заднего α углов; основание канавки делают в форме дуги радиусом rк. Передний угол γ принимают в зависимости от обрабатываемого материала: для стали γ = 10—20°, для чугуна γ = 5—8°. Задний угол на режущих зубьях α = 3—4°, на чистовых α = 2°, на калибрующих α = 1°. Зубья с прямолинейной спинкой применяют для материалов, дающих стружку надлома, с радиусной спинкой — для вязких материалов, дающих сливную стружку. Канавки удлиненной формы применяют при обработке отверстий, прерывистых по длине, а также при большой длине протягивания.